The military rain jacket factory is a bustling hub of activity, where the art of crafting high-quality protective gear meets the demands of modern warfare. Nestled in the heart of an industrial zone, this factory churns out jackets that are not just mere clothing items but are strategic tools designed to shield soldiers from the harsh elements of nature and the unpredictability of battlefields.
As you step inside the factory gates, the sound of machines whirring and workers diligently going about their tasks fills your ears. The air is thick with the scent of treated fabrics and the occasional whiff of adhesives used in the assembly process. Rows upon rows of sewing machines stitch together layers of waterproof materials, creating seams that are not only strong but also flexible enough to allow for maximum mobility.
The production line is a well-oiled machine, each worker playing a critical role in the creation of these essential garments. Pattern cutters deftly maneuver their scissors through rolls of fabric, ensuring that every piece is precision-cut for a perfect fit. Meanwhile, quality inspectors vigilantly examine each jacket, checking for any flaws that could compromise its integrity under stress.
Innovation is at the core of this factory's operations. Engineers and designers work hand in hand to incorporate the latest technology into the jackets. They might be adding new types of insulation that offer better warmth without adding bulk or integrating smart fabrics capable of monitoring environmental conditions and relaying that information back to the wearer They might be adding new types of insulation that offer better warmth without adding bulk or integrating smart fabrics capable of monitoring environmental conditions and relaying that information back to the wearer
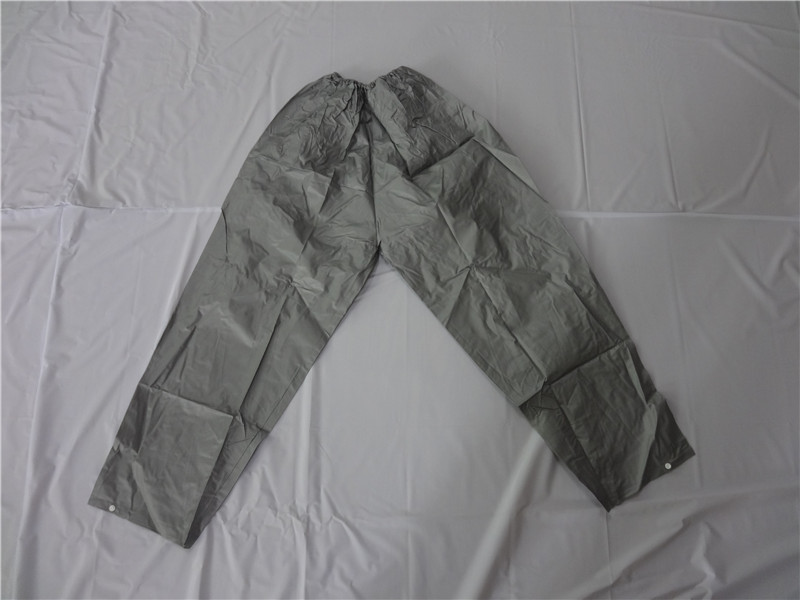
They might be adding new types of insulation that offer better warmth without adding bulk or integrating smart fabrics capable of monitoring environmental conditions and relaying that information back to the wearer They might be adding new types of insulation that offer better warmth without adding bulk or integrating smart fabrics capable of monitoring environmental conditions and relaying that information back to the wearer
military rain jacket factory.
Sustainability is another key focus. The factory strives to reduce waste by recycling fabric scraps and minimizing energy consumption during production. It's a balance between preserving resources and meeting the rigorous standards expected of military gear.
Despite the mechanization, there's an undeniable human touch to the process. Each worker understands the gravity of their contribution—they are not merely sewing threads but weaving together threads of safety and protection for those who serve.
The finished products are then subjected to rigorous testing to simulate various weather conditions and scenarios. Waterproofing, wind resistance, and breathability are all put to the test before any jacket is deemed ready for issue to the troops.
As you leave the military rain jacket factory, you can't help but feel a sense of pride and respect for the craftsmanship and dedication that goes into every piece of equipment manufactured here. These aren't just jackets; they're emblems of a nation's commitment to protect its own, shrouded in the resilience to face the unforgiving rain and the determination to prevail in any climate.